Albemarle
With presence in over 100 countries, Albemarle is a major enabler of lithium-reliant technologies that touch countless facets of people’s lives and entire economies. On engaging BSC Global, Albemale needed to pre-optimize throughput of resources that would flow within a newly planned Lithium Hydroxide processing plant in Kemerton, Western Australia.
THE CHALLENGE
Planning ‘just right’ operational investments
At face value, the challenge seemed straightforward enough. The new plant would be divided into two distinct sections, each processing one of two critical components for producing lithium hydroxide, with each of those sections operating a maximum of five processing trains.
Key goals:
- Effective project cost management
- Optimal plant productivity from day-one
- Sustained resource utilization efficiency
The key question?: Given that the two sections operate at different rates, with different operating and maintenance regimes, how many operating trains would be required for maximizing the plant throughput, without inadvertently, creating cost redundancy and operational bottlenecks?
SOLUTION
Accurately simulating efficiency and value
Before a single piece of new plan infrastructure would be laid, Albemarle needed resolute certainty with reliable, real-world projections of utilization and performance.
To achieve this, BSC proposed and custom-developed a rich model of the entire processing plant anatomy that could be used to test and simulate all possible processing-train configurations under various design rates.
Once actualized, the simulation model outputs would leverage a risk management technique, known as Monte-Carlo analysis, that would consider randomized equipment downtimes to assess variability in performance.
The simulated production outputs would then combine OPEX, CAPEX, and revenue estimates to generate probable profitably values for each of the possible processing-train configurations.
SUMMARY OUTCOMES
Projected 24% increase in project value
The final simulation model developed by BSC was able to accurately predict the likely range and high-level economics required for Lithium Hydroxide Monohydrate production, as well as where in each train-processing configuration bottlenecks were likely to emerge.
The model also showed that, maximizing capacity in the Hydromet section specifically, would yield a project-value increase of as much as 24%.
You might be interested
Woolworths
After opening its first store in 1931, Woolworths has become an iconic presence in South Africa’s retail landscape, serving as a trusted staple for affordable, quality goods. On approaching BSC, Woolworths needed a reliable way of accurately measuring uplift in the Vitality Healthy Food programme - a calculation that would help prevent the over-issuing of rebates to one of their affiliate partners.
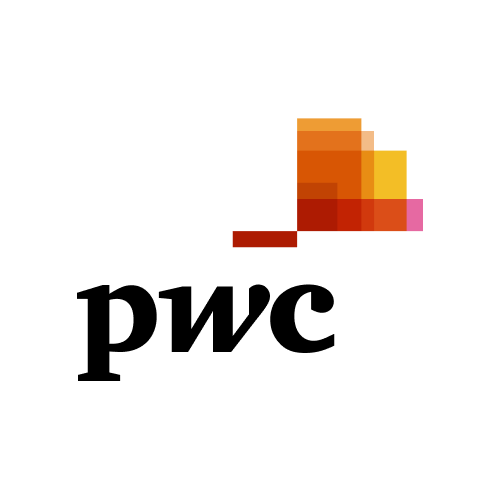
Pricewaterhouse Coopers
NEOM - a 170 km-long eco city with no cars, streets or emissions. That’s the snapshot billing of the proposed Saudi-led project that has attracted global investors as well as the likes of PricewaterhouseCoopers (PwC) who sought BSC Global’s assistance in planning some of the sprawling city assets set to feature as part of the audacious desert mega-city.